RSRG continuously advances in the major Koralmtunnel project.
In the Koralmtunnel project, the Rhomberg Sersa Rail Group demonstrated not only its technical expertise but also its ability to collaborate across different areas.
Together with the consortium partner PORR, the Rhomberg Sersa Rail Group (RSRG) was commissioned by ÖBB to carry out both Lot GU1 (slab track) and Lot GU2 (electrotechnical and mechanical equipment) in the 33 km long Koralmtunnel. Besides the extensive construction components, the main focus is on logistical requirements and coordinating interfaces with different trades and contractors.
For RSRG, this large-scale project provides the opportunity and challenge to develop further in future-relevant areas such as digitization and robotics, in addition to construction aspects, to be prepared for future market requirements and to create a competitive advantage.
Essential to the successful execution of such a complex, multidisciplinary project is the collaboration of various operational units, with the RSRG portfolio "all around the railway" making a significant contribution to the project's success.
In addition to experts from the RSRG project team, RSRG companies Universale Bau and Rhomberg Fahrleitungsbau are also involved in this construction project.
At the Wettmannstätten and St. Paul im Lavanttal stations, Universale Bau, in cooperation with the consortium partner, constructed all the ballast tracks, switches, and loading and washing tracks. The track construction specialist also supported the laying of track and absorber slabs with a gantry crane.
Rhomberg Fahrleitungsbau has also made significant contributions in recent years in the area of electrotechnical equipment and rail power supply on the Koralm route. Recently, the company completed the Lavanttal project. Here, the section from Eis-Ruden to Lavanttal station was equipped with overhead lines and the Granitztal tunnel with a ceiling power rail, including hanging columns, and a substation was constructed at Lavanttal station as an interface between the overhead line and catenary system.
Since March 2024, the company, together with a consortium partner, has been implementing the complete overhead line equipment, including the installation of ceiling power rails, in the two tunnels of the Koralmtunnel over a total length of 66 km. A challenging factor is that only a period of eight months is allocated for the equipment installation. Around 25 employees and six motor tower wagons are working in day and night shifts to complete this task in such a short time. The assembly team is supported by a specially developed assembly train for this construction project.
One logistical challenge is organizing and bringing all the materials into the tunnel. For this purpose, there is a dedicated control center on-site that manages all journeys in and out of the tunnel to ensure a smooth process.
In terms of temporary construction provisions for the Koralmtunnel project, the strength of cross-disciplinary expertise is also evident.
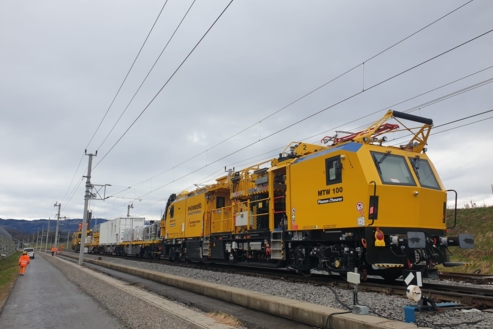
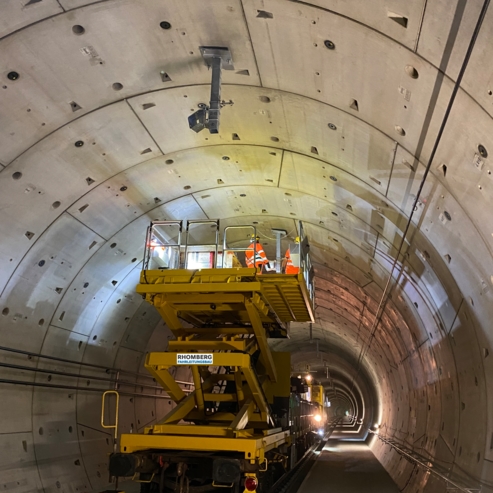
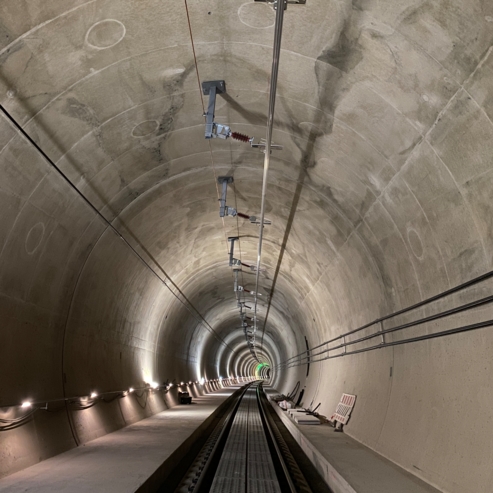
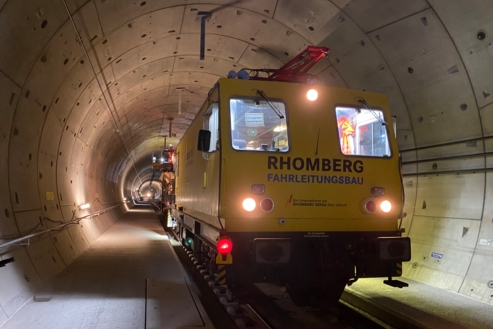
For the construction phase, the construction power supply (medium and low voltage), including construction lighting, communication, access control, and tunnel monitoring, was planned, adapted (handover from raw construction lots), or newly installed by RSRG in collaboration with RSRG subsidiary RS Safetec. Until the completion of the work and the dismantling of the temporary facilities, RSRG is responsible for the maintenance and upkeep to ensure safety in the tunnel.
The main components include:
- Radio systems (fire brigade and operational radio/GSM 900)
- WLAN coverage in the cross passages
- Personnel tracking in the tunnel
- Alarm system and air quality measurement stations
- Integration of sensors (door and gate monitoring, fan control, gate control)
- Various barrier systems with RFID and video surveillance
- Control center equipment
Additionally, in collaboration with RSRG's Digital Rail Services, a train location and switch control system for the logistics handling of construction trains was developed. The construction trains are located outdoors using GNSS (with correction procedures) and inside the tunnel by the installed personnel and vehicle tracking system (BLE-based). Visualization is provided by the partner company bii-GmbH using the software dprob (logistics and construction process planning software), which is also used in other areas.
These software tools for logistics handling were specifically expanded for the electrotechnical equipment (GU2) and are being further developed for goods and storage logistics to ensure that every component is available at the right time and place, ensuring a continuous performance flow.
In terms of robotics, we see the use of a drilling robot, developed with RSRG involvement and undergoing its first test during the handrail installation, as another step into the future.
This shows that RSRG, with its great competence and many ideas and diverse strengths within the group, is very "powerful" and well-positioned for future projects.