Innovative mechanical engineering
With the E3 machines from Bahnbau Wels, the Rhomberg Sersa Rail Group is consistently and successfully pursuing its path to technological leadership.
The two new additions, a Unimat 09-8x4/4S Dynamic E³ tamping machine and a BDS 2000-4 E³ ballast management system, do not only impress with their new external design but also with their environmentally friendly hybrid technology. E³ stands for ‘Economic – Ecologic – Ergonomic’. The most striking difference to the previous generation of machines is the introduction of electricity as a means of supplying energy to the machines. Whenever available, environmentally friendly electricity is drawn from the overhead wires. It is only when there is no catenary power available that all the energy is provided by a generator driven by a diesel engine. This ensures a seamless energy supply to the machines.
Electric braking is also possible with this technology. For this purpose, the kinetic energy is converted into electrical energy via the traction motors and fed back into the network of overhead wires. This is called regenerative braking – the most economical and environmentally friendly way to brake. If there is no possibility of absorbing the electrical braking energy in the network of overhead wires, it is dissipated via braking resistors on the roof. A major advantage is that the shoe brakes are not subjected to thermal stress or wear during purely electric braking.
In addition to their environmentally friendly features, these machines are also characterised by their much lower noise emission. In fully electric operation, they simply whisper.
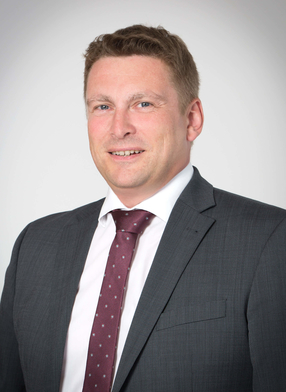
With the Unimat 09-8x4/4S Dynamic E³, further significant innovations have been implemented in addition to hybrid technology, including the special configuration of the tamping units. The ‘8x4’ in the name of the machine already reveals this. Eight individual tamping units, each with four tamping picks, are available for this machine. The units are divided in longitudinal direction, so that besides two sleepers in one operation, individual sleepers can also be processed. The transverse division into four separate units is the basis for full flexibility when working with switches.
Due to a sleeper recognition system for the track area, the operator only needs to take over the cycle control on a per-case basis. This significantly shortens the high concentration periods for the machine operator.
A switch tamping assistant rounds off the machine's comfort. Working on switches is therefore largely automated. This relieves the operator and allows them to focus their full attention on monitoring the tamping process.
With the purchase of the new machines, the Rhomberg Sersa Rail Group not only stays in line with the times, but also sets standards in terms of economy - ecology - ergonomics. Perfect interaction between human and machine optimises the result for the customer – in line with E³